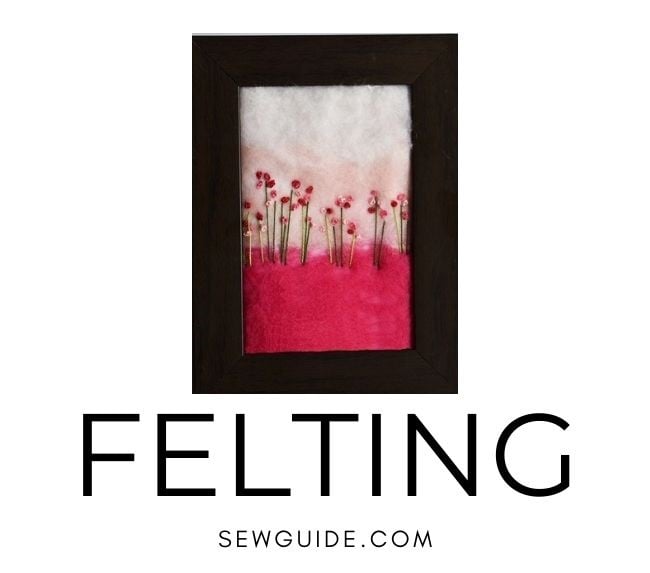
What is felting?
There are 3 types of felting that a fiber/fabric lover does.
1. First is, Felting as a non-woven fabric making process in which fibers are compressed, matted, and joined together, by applying heat, moisture, agitation, and a good amount of pressure. The resultant fabric is called felt, a dense fabric made of permanently interlocked fibers, which does not fray and has an attractive texture that makes it suitable for a variety of sewing and crafting purposes.
Different pieces of felt can be joined together in this way – without a seam. This is usually done for making designs on felt artworks or working on felt toys.
2. Another use of the term is when you use heat moisture and agitation to make a smooth fabric go all fuzzy. If you do not like the smooth look of your sweater and like the fuzzy caterpillar-like look or you want to give a makeover to an old sweater felting it is the way to go.
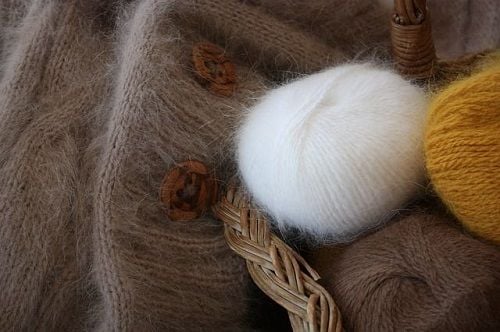
3. The third use of the term is when yarns used for knitting are felted. Here the felting process is used on yarns to make them fuzzy or to join other interesting yarns together to form a single yarn through the help of agitation, heat, and moisture.
Felting creates a beautiful fabric with good bulk and loft, a fabric that does not fray and one that can be used on both sides. You can create whole projects without any seam with feltmaking – for eg., a fitting hat can be made wholly without stitching a single seam. It is also very useful for making clothes and accessories that weather harsh cold climates as the fabric is dense and made of fibers that are very warmth-giving. Another characteristic of a good felt fabric is that once it is made and dried, it will keep its shape no matter what you do to it. Very useful in a lot of projects like hatmaking or 3-d figure making.
History of felting
Today felt is made in factories and you can buy it in stores in all the colors you want but you can make a similar fabric at home using some relevant fibers. Without a doubt, felting is the easiest method of making fabric and because of this wool felt is perhaps the oldest known man-made fabric.
History has records that say that ancient man used felting to make fabric. The Asian nomads knew how to make felt about 5000 years ago. The Romans and Greek also used felt to make tunics, boots, and socks. Sheep’s wool, hair of horse and goat, mohair, and ox (specifically thin short hair) were used to make felt.
How does felting work
In felting, the fibers swell when it gets into contact with hot water. There are small scales on the surface of individual wool fibers which open up when they are washed in hot soapy water. The hairs slide across one another and lock, because of the scales. The fibers entangle with each other and cause the fibers to be matted. Then with agitation and exposure to cold water wool starts to shrink and become dense. The fibers are compressed and matted into a non-woven fabric.
The basic process of felting looks very easy. You just need some water, a heat source, and some fibers to do felting. When all of these are used the fibers get entangled and your nonwoven fabric is made. But then you start doing it and then you like it and then you start reading more about felting and you learn a lot of different other ways to do it – this is when it gets complicated. But nothing to worry about. All easy work if you have dedication to the craft.
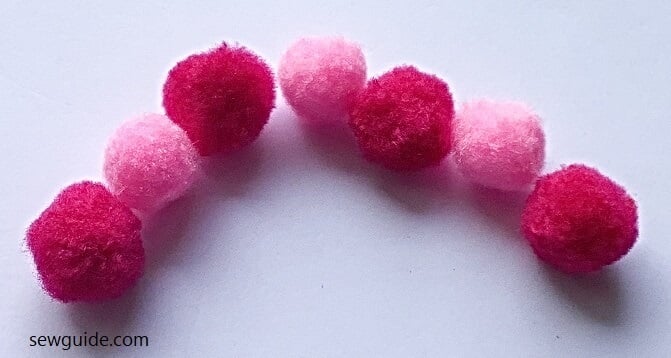
Simple Home Felting Process – step by step
The wet felting method given below is for felting wool fibers into fabric using moisture, some agitation, heat, and pressure. Other than the fiber you are using, the other things that affect the process of felting are the measurement of fiber used, agitation time, and the number of cycles of fulling you will do
The first time you are felting do note these things
- How much fibers are you using – in weight
- How many layers did you use?
- How long did it take for the fibers to matt and then reach the fulling stage
- The dimensions of felt you made with this weight of fibers
- What is the percentage of shrinkage.
1. Decide on the fibers you are using
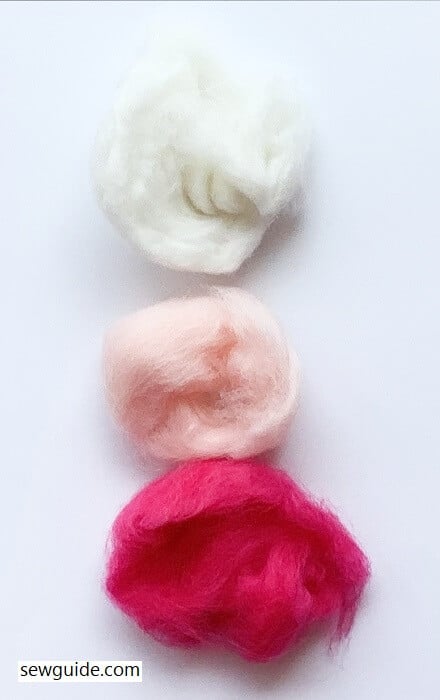
Which fibers are used in felting
You can do felting with potentially fuzzy fibers like wool and acrylic and animal hair and also with cotton, rayon fibers. Pure fibers as well as a mixture of wool and synthetic fibers can be used. A commonly used blend is that of wool and rayon.
Related posts : Types of wool; Textiles in Acrylic; Rayon; Types of fur; Yarns to hand knit a chunky blanket.
But all said and done, wool is still the best fiber for felting. All types of wool including that of sheep, merino, camel, alpaca, and angora are used for felting. All wool fibers do not felt the same way. Fibers of different weights felt in different ways – some become very thick dense felt, some do not. Merino is a fast felting wool which is very soft and a favourite with beginners, though a little expensive than other sheep wool fibers.
Most of the experts use cleaned and carded Wool Roving ie clean, carded unspun Long strands of combed fibers. Wool Batt which is a flat fluffy sheet of wool can also be used.
You can buy fine wool or coarse wool – depending on your project. Fine wool makes a very thick and dense fulled fabric than the medium and coarse wool felt. Fur of Belgian Hares is used to make soft felt which is not at all stiff. Alpaca wool is finer than sheep’s wool. It is also better for making things you will wear (hat, scarves) as it is not as itchy as sheep’s wool
Wool fibers can be mixed with interesting threads using this method.
If you have wool that look dirty or greasy soak them in water with soap for 30 minutes and rinse. Do not agitate when cleaning – you do not want the fibers to start felting already. If you are wet felting you do not need to wash as you will be using soap solution and washing anyway. I have read somewhere that “oil present in wool serve as a natural protection against moths and also help the fibers to fuse together”.
Select the required amount of fibers. This depends on your project. If you are making a hat you need a lot more fiber than if you are making felt flower petals. One thing to remember here is that wool fibers and plant fibers will shrink when wet by at least 20% of their actual size, if not more. If the fibers are synthetic shrinking is not a problem.
2. Decide on the method of felting
The important methods of felting
Felting can be done in different ways according to the kind of agitation used and the materials used for this. The main 2 methods are Dry felting and wet felting
Wet felting
This method uses agitation along with a felting solution made of water and some soap. This is the most used method. You can do wet felting with some liquid soap, hot water, and fibers in a flat vessel
Dry felting/needle felting
This method does not use water at all. It is the best way to work the small details on felted toys, artwork, etc which should not be wet. This is the method to use if you are felting with acrylic fibers.
In needle felting, special barbed needles of different sizes are used to matt the fabric. The fibers are pricked and prodded using the needles on a special padded surface. Needles are used according to the project. The needle jabs and pokes at the fibers repeatedly until everything is entangled and joined together.
3. Gather all your Felting tools
If you are using acrylic fibers you will have to use a dry felting technique. Acrylic fiber is synthetic and can melt in high heat.
Decide on which kind of felting you want to do. If it is wet felting the supplies are different from if you are doing dry felting.
For wet felting: Identify an electric kettle or bathroom geyser or anything that will serve as a continuous source of hot water. You need a surface to do your felting- if it is a small project use a vessel to keep the fibers and do the felting. If it is a big project, small vessels may not be enough. Use thick plastic sheets as a surface. You also need a source of cold water for the rinsing.
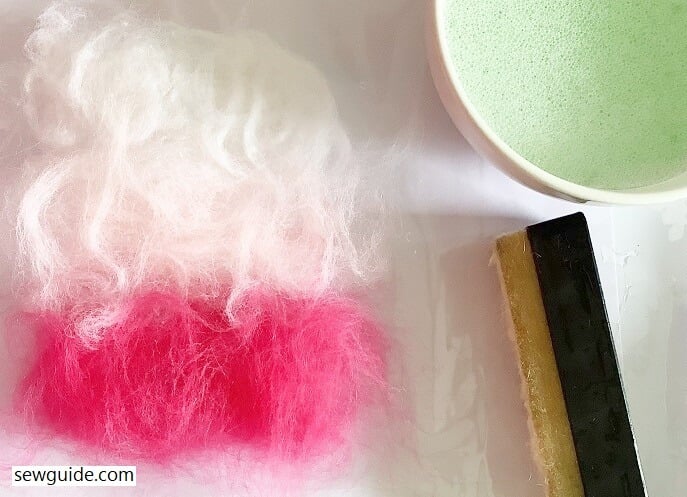
You will also need some liquid soap. Most people recommend using dishwashing liquid for this. They are kept in small bottles ready to be poured into the fibers. If you have only soap, grate flakes out of it and dissolve it in some water.
You also need something to put pressure on the fiber mass like a potato masher or a rubbing tool to rub over the felt when the fibers are entangled. You can use a piece of sponge too. If there are things around your house with a soft ribbed surface you can use them. This is optional though – you can simply use your hand and a good amount of pressure.
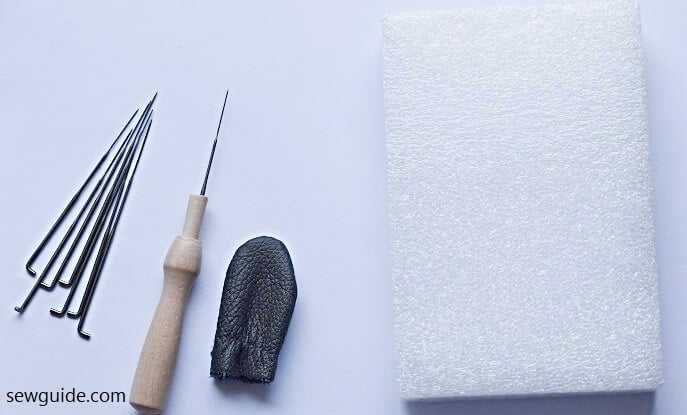
If you have chosen dry felting, you can buy a needle felting kit – this will contain necessary fibers, a number of needles, a surface for felting (to protect your tabletop) and a covering to protect your hands when you are jabbing at your fibers. The top fibers when jabbed at by the needles goes through the bottom fibers matting the whole thing together.
3. Prepare the surface
You can make a flat piece of felt on any flat surface – if you are doing wet felting protect your surface from water and soap. If it is dry felting, protect the surface from the sharp needles.
For a flat piece of felt block an area of your surface for your felt ;For eg if you want square piece of felt, draw the square shape on your surface and make your felt inside this area.
4.Arrange the fibers
Once you have the required amount of fibers, divide it into equal portions – this depends on the thickness you want.
Spread one portion of fibers evenly on your surface along the width of your blocked area (or inside of your vessel or your palm – depending on what you are making).
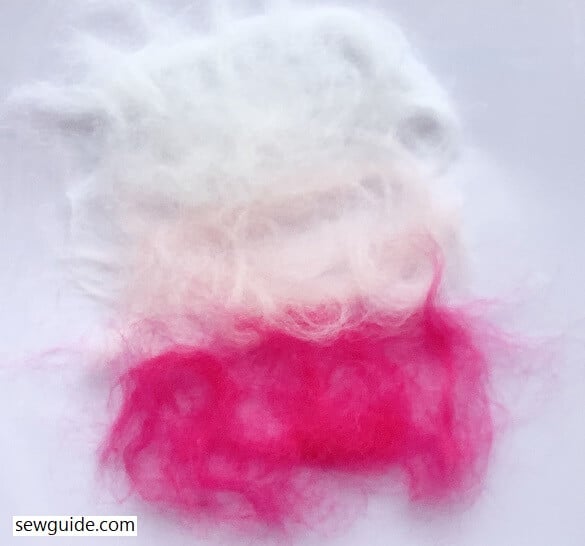
Now, take the second portion and arrange it on top of the bottom layer in such a way that the wool fibers are at a right angle or 90-degree angle to the bottom layer. (If you have single colored fibers you can do this in a single length. As I was looking for an ombre colored effect I had to lay the fibers lengthwise for all colors individually)
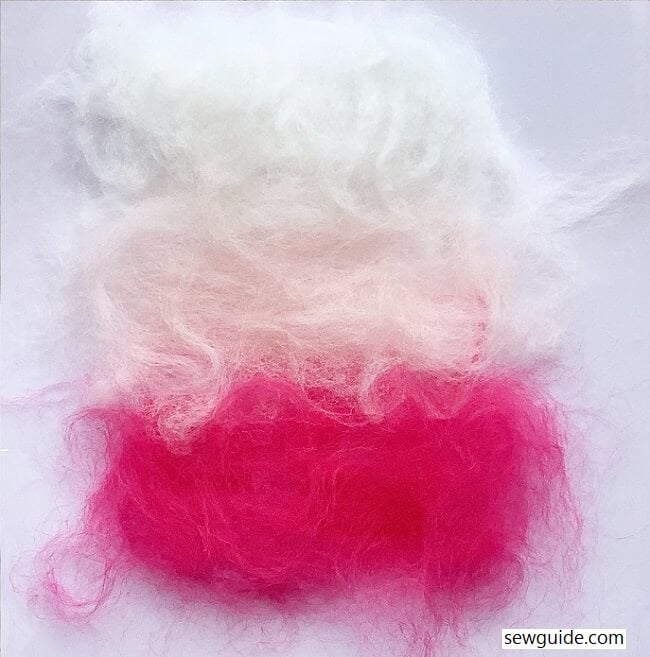
Make as many criss-cross layers as you want on top until the desired thickness is reached. Usually 4 plus layers are made in this way for a soft thin felt. Ensure that the single layers are not too thick randomly resulting in uneven felt. Or that there are no gaps in the fibers – these gaps manifest as holes in your final fabric.
Some recommend using a synthetic netting fabric or thin knit fabric as a top and bottom layer above and below the fibers – this is useful if you have a certain arrangement of fibers and you do not want too much shifting of the fibers and change your design. The netting/thin knit takes in soap water and also helps in turning the felt easily. But make sure that this fabric doesnot get so entangled in your fibers that you cannot take it out. When the felting is completed the fabric will naturally seperate from the netting.
5. Wetting the fibers
Add a small amount of liquid soap to the hot water and gently pour a sufficient quantity of the mixture on top of the wool to wet it. You can periodically pour this hot soapy water on felt or even dip the whole thing.
6. Applying pressure & agitation
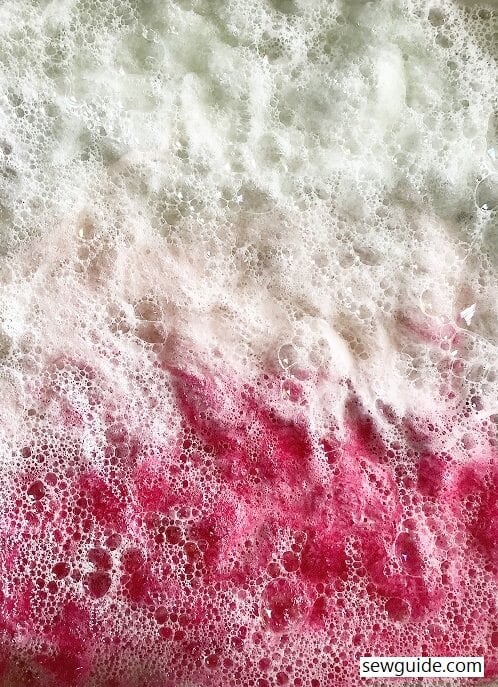
If you are using your hands, press down first and gently massage the fibers from the center to the outsides in circular motion entangling your hands as you go over the soap-covered fiber mass.
But if your hand cannot tolerate the hot water, and you want a lot more agitation, use a tool like a potato masher, washboard, or a duster as I have done (something thing with abrasive properties), press down the wool to on your surface and get all the air out and roll it over. Add more hot water to drown the wool. Work from the edges by pressing until all of the wool is wet and matted down.
Gently rub in circular motions on the surface and agitate the wool. This speeds up the interlocking process. Press gently at intervals to remove air and make the felt denser.
Do you know that you can felt fibers inside a washing machine – but it is not said to be a reliable method as the process is not totally in your control. But if you have large amounts of fibers and you are short of time and labour, well— any shortcut is considerable.
7. Turning
After agitation of one side of the fibers, you have to turn it over and do the same with the other side. Carefully lift the matted wool and turn it over. Add more soap water and repeat the pressure and agitation as earlier. You can do this, again and again, to maintain the evenness on both sides.
8. Rinsing
Pour out the soapy water from the matterd fabric and run cold water over the matted fibers. Some use a little vinegar in the final rinse. Now press the water out of it and you can see your felt forming already.
Try to pinch your newly made felt in between your hands – at this stage the individual fibers should not separate and come out when you pinch.
9. Fulling & Palming
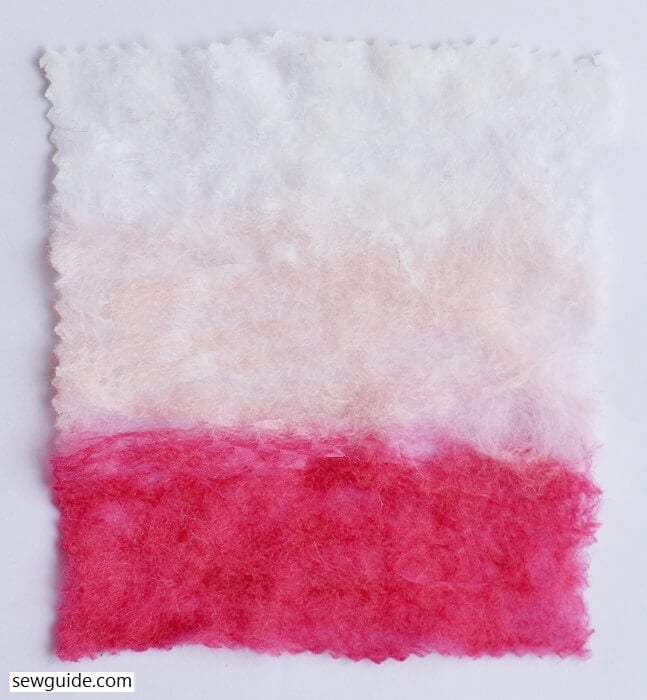
Fulling is done to create a fuller more denser fabric. This step is also the shrinking stage which tightens up the felt and also the thickening stage as the felt becomes thicker and denser the more you do this. Palming is done to full the felt.
Palming refers to the process of rubbing the felt in between the palms or with some other tool. The felt is made into a loose roll between your palms or in between netting if you are using it. Squeeze out all excess water (no wringing). Roll in the other direction and repeat the process. The more you do it, the denser it becomes.

10. Drying
Once you are satisfied with your fulling result, it is time to dry the felt. Air drying is best.
You can make patterns on your felted fabric in many ways – small pieces of colored wool can be incorporated into the felting and made to be a part of the pattern of the fabric. Other methods are applique, embroidery and painting.
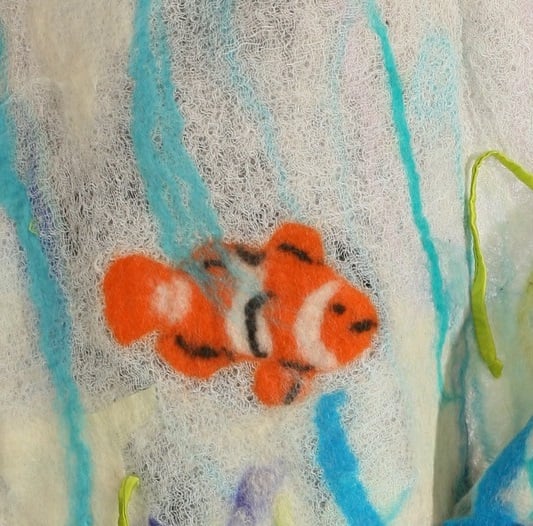
If you have a single craft bone in your body you will be interested in felting, because it is very easy to do and it is also very inexpensive to complete, if you have the fibers and the resultant fabric is beautiful. You can use this method to make individual projects like coats, boots, jewelry, coasters, 3-d sculptures, carpets and mats, pincushions, balls, and a whole lot more. Applique using handmade felt is beautiful. There are many many other things that you can make with your own DIY felted fabric. The possibilities are endless.
Related post :Different types of felt; How to make Felted beads.; Make felt flowers; How to make felt roses
Books to read for more knowledge :
- How to Make Felt – by Anne Belgrave
- Feltmaking: Techniques and Projects by Inge Evers